Seam welding is a specialized welding process in which two or more overlapping metal sheets are joined together using a series of overlapping welds, creating a continuous, leak-proof seam. This is achieved using rotating wheel-shaped electrodes that roll over the workpiece while applying pressure and an electric current.
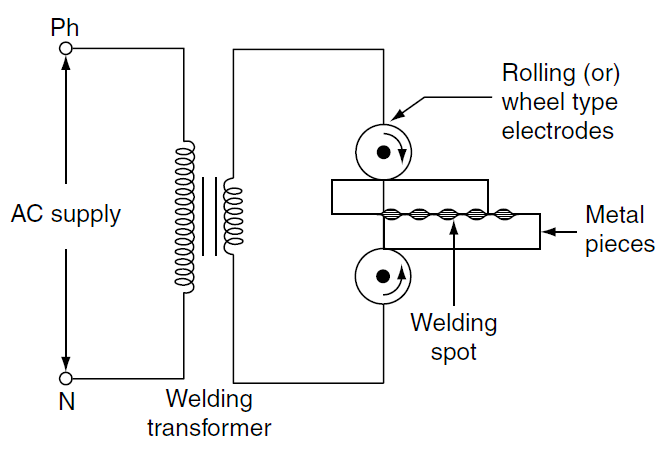
Key Components of Seam Welding
- AC Supply: Provides electrical power for the welding process.
- Welding Transformer: Converts high-voltage AC power into low-voltage, high-current power needed for welding.
- Wheel-Type Electrodes: Rotating disc-like electrodes that apply pressure and conduct the welding current to the workpiece.
- Metal Pieces: The materials being welded together.
- Welding Spot: The location where heat is generated and the metal fuses together due to the current flow.
Seam Welding Process
- Preparation: The metal sheets are cleaned to remove dirt, oil, and oxides for better weld quality. The sheets are overlapped and positioned between the rotating wheel electrodes.
- Welding: The electrodes are pressed against the metal sheets while rolling over them. An electric current is passed through the electrodes, generating heat due to electrical resistance at the contact points between the sheets. The heat melts the metal, creating a weld nugget. As the electrodes roll forward, overlapping nuggets form a continuous seam.
- Cooling: Proper cooling ensures the weld does not overheat, maintaining the integrity of the material.
Types of Seam Welding
- Roll Spot Welding: Produces intermittent weld spots instead of a continuous seam.
- Continuous Seam Welding: Creates a leak-proof seam by producing overlapping weld nuggets.
- Micro Seam Welding: Used for precision applications, such as in electronics.
- Foil Seam Welding: Ideal for welding thin metal foils.
Advantages of Seam Welding
- Produces strong, leak-proof joints.
- High-speed welding process suitable for mass production.
- Consistent and uniform weld quality.
- Can handle thin sheets of metal effectively.
Disadvantages of Seam Welding
- Limited to straight or slightly curved seams.
- Equipment is bulky and expensive.
- Not suitable for thick materials.
- Requires precise alignment and preparation of workpieces.
Applications of Seam Welding
- Manufacturing of fuel tanks and drums.
- Automotive industry (e.g., mufflers, wheels).
- Construction of radiators and heat exchangers.
- Food and beverage containers (tin cans).
- Aerospace components requiring leak-proof seams.
Hi, I think your site might be having browser compatibility issues. When I look at your website in Safari, it looks fine but when opening in Internet Explorer, it has some overlapping. I just wanted to give you a quick heads up! Other then that, fantastic blog!
Your comment is awaiting moderation.